Streamlining large-scale data management
Our client, a manufacturer in the pulp and paper industry, was facing a significant challenge: from an operational perspective, they were lacking real-time data for an evolving market. Having never been linked together, their factories were operating like independent companies with their own methods and machines. It was impossible to compare the productivity of one site to another.
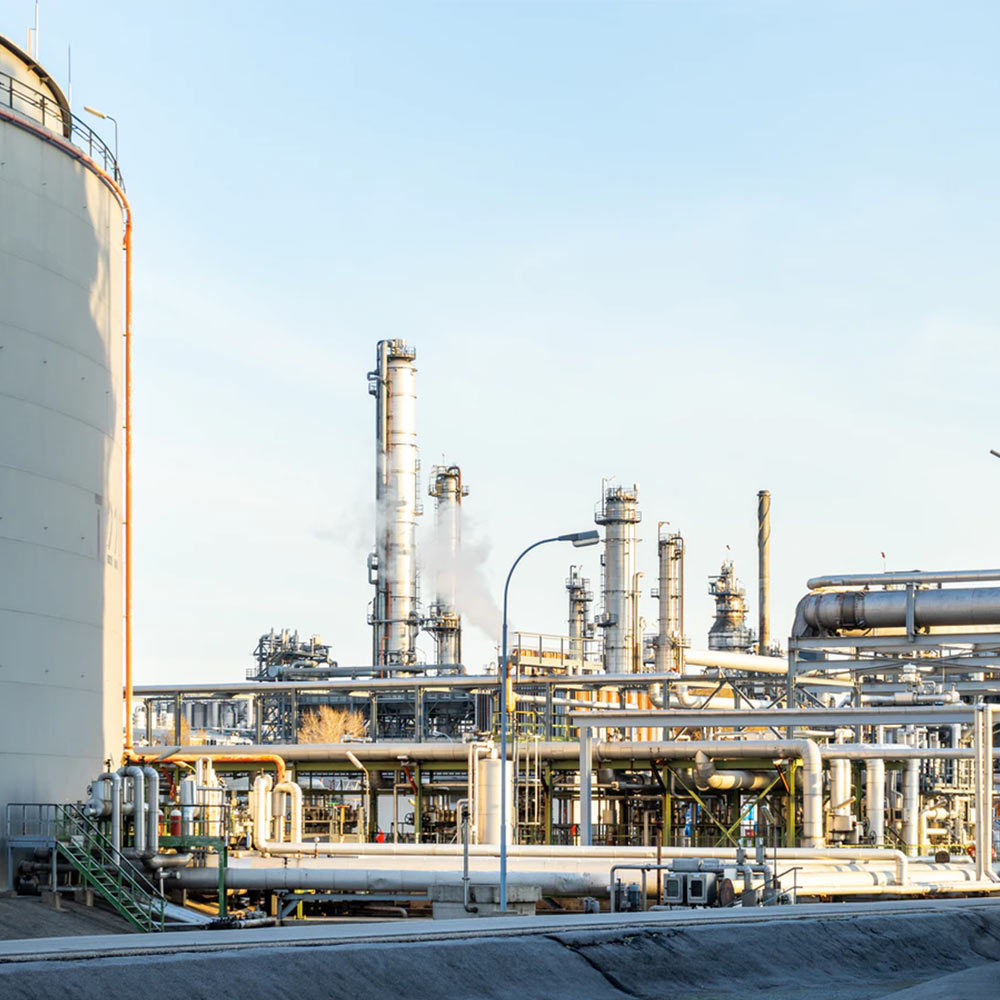
Our mission : upgrade the production line to increase visibility
In order to provide management with a unified vision to facilitate data-backed decision-making, we had to take the company’s four operational axes into account: measuring production downtime and slowdowns, analyzing more than 125 metrics related to their production equipment using IOT, verifying the efficiency of their energy recovery processes and monitor raw material transformation throughout cycle. From analyzing the client’s business to building our solution, we brought in a diverse group of experts for a flexible, collaborative approach that helped us design a model combining the client’s current processes and business intelligence needs. To accomplish this, we carried out the following:
- Study of current methods,
- Optimization of analytical chain, from data source to decision-makers,
- Creation of a canonical model to collect, process, and streamline data,
- Integration of new solutions via active change management,
- Creation of clear visualization and modelling templates.
The key to success: agile co-development
At agileDSS, we believe that change management is just as important as technical development. For this particular project, this belief was our guiding light: given how many processes were in play, going back to square one and creating an entirely new system was out of the question.
Our human approach is what makes us different. To make sure that the model we implement yields the desired results, we first need to ensure that the people on the ground are embracing the change.
Benefits of integrating our revolutionary solution
The unified data platform that we developed for our client resulted in integrated plants operations, thanks to:
- Effective, durable analytical structure,
- Standardized data management,
- New ability to identify problems,
- Reliable production data archive,
- Global view of data that can be segmented.
Technological environment
- Oracle
- Microsoft BI (SSIS, SSAS)